I know some have used an LA B&M flexplate with a magnum 5.9 and claim not to have any terrible vibration issues but I would not want to do it.
I tried to come up with a fairly easy solution to this problem without doing any welding.
Shown here is an LA 360 to 904 trans B&M flexplate that has a basic radius of 5.42" and is made of .125" steel. Based on these numbers I calculated the size and centroid of a section (directly opposite the existing negative offset) that could be cut out with a band saw to reduce the offset weighting by 5.14 ounce inch. 5.14 oz-in is the difference between factory LA and magnum offset ballance of flexplate/flywheel.
Measure as close as you can a "cord" that is 4.766" and directly opposite existing cutout. Note that the height of this section from cord to radius peak is about .552". It is unlikey that you will hit these numbers exactly with typical tools but I didnt want to round my theoretical numbers.
After cutting this section out the flexplate should match factory 360 magnum flexplate offset weighting.
Note: I have checked my math a few times and am fairly confident of numbers but havent needed to try one out yet. Also I have not had one checked on a balancer. The numbers given only apply to the 904 flexplate, the B&M 727 flexplate has a larger radius and the area to be cut would be different.
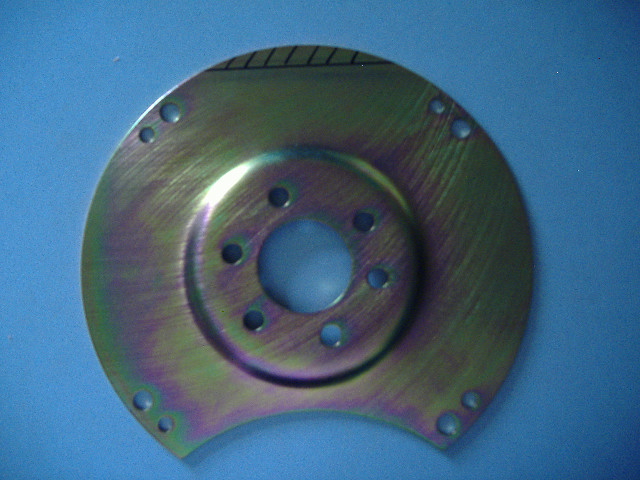
Last edited by Rapid340; 10/03/15 03:30 PM. Reason: no balancer check