Moparts
Subframe connector options and opinions
Posted By: Kern Dog
Subframe connector options and opinions - 01/20/12 06:44 AM
Being the frugal guy that I have been for years, the last 2 sets of subframe connectors that I have installed have been homemade using 3x3 .120 stock cut to fit. I welded both sets in, both were A body cars. Now I am ready to do this in the Charger. When I painted the car in 2003, I sprayed the underside to match the topside. This means that when I weld whatever connectors into place, My welds will need to be cleaned up and everything will get painted body color.
I have seen all sorts of different types of connectors in Mopars. The 2x3 bolt in type seem to be the least effective but offer the most ground clearance. In theory, I like the look of the XV contour fit units, but they appear to be only 3 sided. How effective can that be? I'll guess that they intend the edges to be welded to the floorpans? I'd bet that their units are thicker than the guage of the floorpans, so what would you recomend as far as welding two sections of metal of different thicknesses?
I spent $44 for 3x3 plus cutting & grinding discs to make the A body connectors. They are welded on 3 sides at the T-bar crossmember and 3 sides at the rear frame rail. My thinking is that being boxed rather that 3 sided, these should be stronger.
I'm interested in seeing pictures and reading about other members connectors. It may help me decide which way to go. Thanks.
Posted By: astjp2
Re: Subframe connector options and opinions - 01/20/12 08:40 AM
The floor pan boxes in the weld in XV style, they remain rigid if they cant flex. Not a big deal. Tim
Posted By: jcc
Re: Subframe connector options and opinions - 01/20/12 03:29 PM
The first question should be IMO, could someone describe and BACK UP at least, with sound reasoning, what actual forces sub frame connectors resist? I am not questioning many many positive reports of thier improvements in ride etc. So are they resisting compression as the rear leafs push forward upon acceleration, are they resisting twist individually, if just under tension we can just use a steel cable, are they preventing a bending moment as front of leaf pushes up upon acceleration with a bending moment provided by the front mass of the car, ie engine, etc, are they just straightening out the force path thru 4 right? angle turns from the front hanger to the doorsills back to the TB crossmember, etc?.
If we knew what they are resisting, it would be a lot easier to design a solution. I suspect they are doing all the above, but some more then others, but which one? Say if twist was the main force, a large dia tube would be first choice, if bending moment, a tall I beam, yaw? bending, an I beam on its side, etc. My understanding is it needs to be the smallest and lightest shape/size that gets the job done. Anyone can oversize a solution, only a smart designer knows just how much is needed, if you way oversize, you look.....?
Years back member AAR? (patent attorney) had a lengthly thread on Subframe connectors, and main conclusion was the larger the crossection of the subframe, the stiffer, wall thickness provides a lot less stiffness then crossection increase gives. The installation advantages are numerous with the contour cut-out connectors, and installation ease IMO is thier only advantage. Performance wise, compared to a full tube they leave a lot on the table.
Posted By: dangina
Re: Subframe connector options and opinions - 01/20/12 03:36 PM
Brads70 from protouring mopar offered this idea from his ride which I'll be doing myself - its 1x2" 0.90 tubing with tubes added for strength:
Posted By: domingo
Re: Subframe connector options and opinions - 01/20/12 06:51 PM
way i do em
Posted By: domingo
Re: Subframe connector options and opinions - 01/20/12 06:53 PM
2" x 2" sqare tube 3mm tick wall.
i dont go rectangular because it prtrudes too much into the pass compartment, rectangular is for a race car only IMO.
On an e body I will only cut the rear floor pans to the point that the portion that prtrudes into the pass compartment can be hidden with padding on the sides and then carpet on.
Posted By: domingo
Re: Subframe connector options and opinions - 01/20/12 06:55 PM
I go thru the trans cross memeber and weld to the front frame rails...much better than what anybody else offers you out there.
Posted By: domingo
Re: Subframe connector options and opinions - 01/20/12 06:56 PM
I also use torque boxes on all 4 corners. You can get them thrugh the link in my signature.
Posted By: Viol8r
Re: Subframe connector options and opinions - 01/20/12 06:59 PM
Save up and buy the Hotchkis connectors. Takes about 2 hours to install and you don't to hassle with modifying the floor, interior or even your e-brake cable.
Posted By: dangina
Re: Subframe connector options and opinions - 01/21/12 02:07 AM
Quote:
I go thru the trans cross memeber and weld to the front frame rails...much better than what anybody else offers you out there.
looks great
is it bad to cut through you tranny crossmember? would it be better to run the subframe brace to the transmission crossmember on one side, and then to the frame rail on the other side?
Posted By: Kern Dog
Re: Subframe connector options and opinions - 01/21/12 02:17 AM
Quote:
Quote:
I go thru the trans cross memeber and weld to the front frame rails...much better than what anybody else offers you out there.
looks great
is it bad to cut through you tranny crossmember? would it be better to run the subframe brace to the transmission crossmember on one side, and then to the frame rail on the other side?
I was thinking the same thing. Maybe if the car is a bare shell, cutting through the T bar crossmember may not pose a problem. I like the way it looks though.
Posted By: Kern Dog
Re: Subframe connector options and opinions - 01/21/12 02:32 AM
I was also interested in seeing photos of factory or custom torque boxes installed in the car. I understand that they were factory instelled on Hemi and convertible cars, but until now I never paid much attention to them.
Posted By: domingo
Re: Subframe connector options and opinions - 01/21/12 04:09 AM
Quote:
Quote:
I go thru the trans cross memeber and weld to the front frame rails...much better than what anybody else offers you out there.
looks great
is it bad to cut through you tranny crossmember? would it be better to run the subframe brace to the transmission crossmember on one side, and then to the frame rail on the other side?
Its MIG welded all around, how could it possibly be weaker???
You can do it either way really, it doesnt matter. as long as you cut and then weld everything, its as strong or stronger than before because now the crossmember has a bigger area (the connector) to spread the forces the torsion bar inflicts on it. Either way you see it is stronger all the way.
Posted By: curleysracecars
Re: Subframe connector options and opinions - 01/21/12 04:22 AM
No worries welding two different thicknesses of metal...they wont be much different anyways. The 3 sided units are probably comparable to a 4 sided tube, but you will pay for them obviously. I REALLY like the idea of going through the Tbar crossmember and tieing them back into the frame rails. I have been thinking about building some as a production product...maybe I can make an option that goes through the crossmember.
By the way, where in Granite Bay are you? Small town...we cant be too far away. LOL.
Posted By: Kern Dog
Re: Subframe connector options and opinions - 01/21/12 05:52 AM
I'm near Folsom Lake, not too far from the dam.
PM me if you want. I'm a member of the Capital City Mopars car club. We always welcome visitors as well as new members!
Posted By: HUSTLESTUFF
Re: Subframe connector options and opinions - 01/21/12 08:03 AM
I like the hotchkis style as it kinda does away with the need for torque boxes. It in reality, transfers the "load" from the rear end to the front of the car. It also ends up at the front frame rail vs off to the side. I just made a set for my 74 Petty Clone. I used 1 1/2 x 1 and welded two together so I have 1 1.2 x 2. Probably $35 in materials. Franky, Come on up to Orland if you want to build a set. Mike
Posted By: ScottSmith_Harms
Re: Subframe connector options and opinions - 01/21/12 08:22 AM
Orland! I went to high school in Willows!
Posted By: Pale_Roader
Re: Subframe connector options and opinions - 01/21/12 11:44 AM
Domingo definitely has the aesthetic vote... looks like the factory built it. That was one ov my options.
The other option was the contoured cut-out, weld to floor version. I would think that keeping the stronger 2x3 piece intact and cutting through the weaker floor sheetmetal would be stronger though. I'd also like a lower profile connector than both ov these ideas... my exhaust is going out the side T/A style.
Hmmm...
Posted By: Anonymous
Re: Subframe connector options and opinions - 01/21/12 03:38 PM
Quote:
The first question should be IMO, could someone describe and BACK UP at least, with sound reasoning, what actual forces sub frame connectors resist? I am not questioning many many positive reports of thier improvements in ride etc. So are they resisting compression as the rear leafs push forward upon acceleration, are they resisting twist individually, if just under tension we can just use a steel cable, are they preventing a bending moment as front of leaf pushes up upon acceleration with a bending moment provided by the front mass of the car, ie engine, etc, are they just straightening out the force path thru 4 right? angle turns from the front hanger to the doorsills back to the TB crossmember, etc?.
If we knew what they are resisting, it would be a lot easier to design a solution. I suspect they are doing all the above, but some more then others, but which one? Say if twist was the main force, a large dia tube would be first choice, if bending moment, a tall I beam, yaw? bending, an I beam on its side, etc. My understanding is it needs to be the smallest and lightest shape/size that gets the job done. Anyone can oversize a solution, only a smart designer knows just how much is needed, if you way oversize, you look.....?
Years back member AAR? (patent attorney) had a lengthly thread on Subframe connectors, and main conclusion was the larger the crossection of the subframe, the stiffer, wall thickness provides a lot less stiffness then crossection increase gives. The installation advantages are numerous with the contour cut-out connectors, and installation ease IMO is thier only advantage. Performance wise, compared to a full tube they leave a lot on the table.
Aren't the factory rockers in effect thick gauge sorta-square tubes connecting the front and rear subframes? If so, what do aftermarket subrame connectors do that they don't? Just add strength to the connection because you now have four subrame connectors instead of two? Perform some other function?
And although it might present clearance issues for driveshaft and/or exhaust, wouldn't an X-shaped subframe connector be much more rigid than two straight tubes?
Posted By: jcc
Re: Subframe connector options and opinions - 01/21/12 03:42 PM
Quote:
I go thru the trans cross memeber and weld to the front frame rails...much better than what anybody else offers you out there.
yes, I like that, simple, clean, direct path for load transfer, no goofy add on's, reinforces TB load point
Posted By: jcc
Re: Subframe connector options and opinions - 01/21/12 03:53 PM
Quote:
Quote:
The first question should be IMO, could someone describe and BACK UP at least, with sound reasoning, what actual forces sub frame connectors resist? I am not questioning many many positive reports of their improvements in ride etc. So are they resisting compression as the rear leafs push forward upon acceleration, are they resisting twist individually, if just under tension we can just use a steel cable, are they preventing a bending moment as front of leaf pushes up upon acceleration with a bending moment provided by the front mass of the car, ie engine, etc, are they just straightening out the force path thru 4 right? angle turns from the front hanger to the doorsills back to the TB crossmember, etc?.
If we knew what they are resisting, it would be a lot easier to design a solution. I suspect they are doing all the above, but some more then others, but which one? Say if twist was the main force, a large dia tube would be first choice, if bending moment, a tall I beam, yaw? bending, an I beam on its side, etc. My understanding is it needs to be the smallest and lightest shape/size that gets the job done. Anyone can oversize a solution, only a smart designer knows just how much is needed, if you way oversize, you look.....?
Years back member AAR? (patent attorney) had a lengthly thread on Subframe connectors, and main conclusion was the larger the crossection of the subframe, the stiffer, wall thickness provides a lot less stiffness then crossection increase gives. The installation advantages are numerous with the contour cut-out connectors, and installation ease IMO is thier only advantage. Performance wise, compared to a full tube they leave a lot on the table.
Aren't the factory rockers in effect thick gauge sorta-square tubes connecting the front and rear subframes? If so, what do aftermarket subrame connectors do that they don't? Just add strength to the connection because you now have four subrame connectors instead of two? Perform some other function?
And although it might present clearance issues for driveshaft and/or exhaust, wouldn't an X-shaped subframe connector be much more rigid than two straight tubes?
IMO you are correct, add on sub frame connectors are just straighter factory rockers, on steroids.
An "X" design is usually just a replacement for a flat shear plate, for many reasons, some obvious, but an X would mainly be beneficial in this application would be if a force was being say applied by only one wheel during acceleration, and therefore trying to "shear" the car, however if an "x" was on four planes, bottom, top, sides, you would then have a very large "tube", and that would resist greatly any twist/torsion forces, which is of choice what most race cars accomplish with a full cage, but an x on one side doesn't seem to me get very much buck for bang.
Posted By: JAMESDART
Re: Subframe connector options and opinions - 01/21/12 04:28 PM
i used the uscartool connectors on 2 cars. i think they are way over priced for a frame connector, compared to how cheap you can buy a length of tube, but they are really nice. weld to the floor pan from the front cross member all the way back to the rear rails.
Posted By: domingo
Re: Subframe connector options and opinions - 01/21/12 04:51 PM
No way the Hotchkis connectors are better than what I did on my car.
Ground clearance is defintely better on mine.
Also rigidity is way superior, even when Im just using 2" x 2" square tube.
Mine look like if it was a factory deal really....
I also cut the rear frame rails some so that the connector tucks in some....it isnt welded under the frame rail.
Posted By: domingo
Re: Subframe connector options and opinions - 01/21/12 04:53 PM
...
Posted By: domingo
Re: Subframe connector options and opinions - 01/21/12 04:54 PM
more...
Posted By: domingo
Re: Subframe connector options and opinions - 01/21/12 04:56 PM
see how a section of the rear frame rail is cut...also, the E brake brackets need to be modified a bit, but they stay on the factory location and work just like factory. Everything will bolt of afterwards. And the fron sections that tie on the front frame rails do not get in the way of anything.
Posted By: domingo
Re: Subframe connector options and opinions - 01/21/12 04:58 PM
mocking up. The e bodies do not have the rear frame rails parallel to the rockers, so you need to incorporate a kink on the tube by cuttong a slice and welding....same for the kink for the front frame rail ties.
Posted By: domingo
Re: Subframe connector options and opinions - 01/21/12 05:00 PM
mocking up
Posted By: domingo
Re: Subframe connector options and opinions - 01/21/12 05:01 PM
VIEW FROM THE OTHER END
Posted By: domingo
Re: Subframe connector options and opinions - 01/21/12 05:03 PM
protrusion in the passenger compartment is minimal. Jute padding on the sides and carpet on top will take care of it and the interior will look factory.
Posted By: domingo
Re: Subframe connector options and opinions - 01/21/12 05:10 PM
e brake bracket that needs to be modified....thats it!
Then if you want to you add the torque boxes I sell below and YOU ARE ALL SET. Super strong and you dont ruin your car as this is a mod I dont think you will regret or that will prevent you from enjoying your car as if it was unmodified. You can use your e brake cable, you have leg room on the rear seat, etc.
I do steer away from cutting up or modifying my cars, speciually if they are street cars. Of course I would not do this to an original HEMI car, or an RT or something rare....because you are cutting and welding. But on all my "clone", "tribute" or modified cars I do this. Its a nice upgrade and you cant really tell they have been modified unless you really know how these cars look from, the underside from the factory.
I was thinking about offering these connectors already bent, trimmed and ready to install, along with the modified E brake brackets to go along with my torque boxes offerings....
What do you guys think?
Posted By: ThermoQuad
Re: Subframe connector options and opinions - 01/21/12 07:49 PM
Domingo, nice work!
Now I suggest weld up the rest of the car. I can tell you that welding up it works wonders, esp underneath. Just be careful not to set the seam sealer on fire. The black n blue charger had a lot of welding underneath where it counts...and a fire.
Another overlooked area is a reinforcement across the package tray that is needed for those 5 pt seat belts and as another benefit stops all the flex across there. Go a step further and weld up the V brace as well. I think you can glue in the reinforcements as well with the correct glue.
Weld weld weld and weld some more.
If you weld up or glue enough of the car in the critical areas it will become enough of a true "unit" body and handle like a caged race car. The f-a-s-t race guys found the cars reacted better with a cage and no frame ties.
Now take it the rest of the way and put a bolt in "race brace" across the shock towers and back to the firewall and reinforce the stock braces in the wheel wells on the inner fenders. Weld the area where the uca mounts are welded to the car and weld up the shock towers and inner fenders. Don't forget a fully welded K frame. I am not sure the lower radiator brace is required bit it won't hurt either to weld that up.
Posted By: boydsdodge
Re: Subframe connector options and opinions - 01/21/12 10:00 PM
I think they look great, nice work.
Posted By: Kern Dog
Re: Subframe connector options and opinions - 01/21/12 11:14 PM
Thanks for posting, Domingo. Great idea, great execution.
Posted By: HUSTLESTUFF
Re: Subframe connector options and opinions - 01/22/12 02:30 AM
Quote:
No way the Hotchkis connectors are better than what I did on my car.
Ground clearance is defintely better on mine.
Also rigidity is way superior, even when Im just using 2" x 2" square tube.
Mine look like if it was a factory deal really....
I also cut the rear frame rails some so that the connector tucks in some....it isnt welded under the frame rail.
I agree those are about the best I've seen, but your building the car. Frankenduster's car is painted underneath and I was just trying to minimize the on car welding. Mike
Posted By: jcc
Re: Subframe connector options and opinions - 01/22/12 02:42 AM
Quote:
The f-a-s-t race guys found the cars reacted better with a cage and no frame ties.
, is that comparing a car with a cage and no frames ties, with a car just with just frame ties, or is that comparing car with a cage and no frame ties to a car with a cage and frame ties?
Still interesting comment regardless.
Posted By: NITROUSN
Re: Subframe connector options and opinions - 01/22/12 03:49 AM
I went with the us car tool frame ties. They each required an hour or so to get the fit right. Every floor pan is slightly different. I slotted the sides for e-brake cable routing. No other mods needed. Not sure on how the brake and fuel lines are going to fit. Very tight clearance. Here are a few pics.
Posted By: NITROUSN
Re: Subframe connector options and opinions - 01/22/12 03:49 AM
2
Posted By: NITROUSN
Re: Subframe connector options and opinions - 01/22/12 03:50 AM
3
Posted By: NITROUSN
Re: Subframe connector options and opinions - 01/22/12 03:50 AM
4
Posted By: NITROUSN
Re: Subframe connector options and opinions - 01/22/12 03:51 AM
5
Posted By: NITROUSN
Re: Subframe connector options and opinions - 01/22/12 03:51 AM
6
Posted By: NITROUSN
Re: Subframe connector options and opinions - 01/22/12 03:53 AM
7 I also bought the torque boxes from Domingo.
Posted By: jcc
Re: Subframe connector options and opinions - 01/22/12 04:10 AM
Here's a pic of the right side front detail of a 72 Dart frame connector tie in to the TB Crossmember. I'm installing a cage in this car, so I also added an outrigger/gusset to support the roll bar mounting plate. One issue with the typical frame connectors IMO is they mount to the side of the TB crossmember, and nothing really internally transmits force forward, I welded up the inside spot welds, I added two internal gussets, and the welded in oval tube is for 2 fuel line's passage. I do think Domingo's solution is a more robust and audacious solution to the problem at hand.
Posted By: astjp2
Re: Subframe connector options and opinions - 01/22/12 07:06 AM
Do you have any pics of the package tray mods or the race brace across the shock towers? Thanks Tim

Quote:
Domingo, nice work!
Now I suggest weld up the rest of the car. I can tell you that welding up it works wonders, esp underneath. Just be careful not to set the seam sealer on fire. The black n blue charger had a lot of welding underneath where it counts...and a fire.
Another overlooked area is a reinforcement across the package tray that is needed for those 5 pt seat belts and as another benefit stops all the flex across there. Go a step further and weld up the V brace as well. I think you can glue in the reinforcements as well with the correct glue.
Weld weld weld and weld some more.
If you weld up or glue enough of the car in the critical areas it will become enough of a true "unit" body and handle like a caged race car. The f-a-s-t race guys found the cars reacted better with a cage and no frame ties.
Now take it the rest of the way and put a bolt in "race brace" across the shock towers and back to the firewall and reinforce the stock braces in the wheel wells on the inner fenders. Weld the area where the uca mounts are welded to the car and weld up the shock towers and inner fenders. Don't forget a fully welded K frame. I am not sure the lower radiator brace is required bit it won't hurt either to weld that up.
Posted By: Rick_Ehrenberg
Re: Subframe connector options and opinions - 01/22/12 04:48 PM
Quote:
Aren't the factory rockers in effect thick gauge sorta-square tubes connecting the front and rear subframes? If so, what do aftermarket subrame connectors do that they don't? Just add strength to the connection because you now have four subrame connectors instead of two? Perform some other function? <snip!>
I thought the same for decades. The I started to notice that newer Mopars -- every B-van, Cherokee, Neon, Stratus, etc. had what was effectively "frame connectors" from the factory, which they started referring to as "uniframe" design. So I give some simple 2X2" tubing a shot (A-body). Holy cow, the first block, I was fairly well freaked out. The difference in platform rigidity was instantly noticeable.
2X3" (slit the floor) is obviously even better.
The sawtooth ones are surely a cleaner installation, but are only as strong as the narrowest point.
Take your pick. But do something! You'll never look back!
Rick E.
Posted By: kielbasa
Re: Subframe connector options and opinions - 01/22/12 11:10 PM
I myself would love to do something, but what options exist for those of us that those of us (for fear of ruining the cars value) have a hard time with cutting into our cars?
I'd love to stiffen up my AAR, but cringe about welding into it.
Posted By: jcc
Re: Subframe connector options and opinions - 01/23/12 12:42 AM
Just wave as we go by you
Posted By: autoxcuda
Re: Subframe connector options and opinions - 01/23/12 02:00 AM
Quote:
I myself would love to do something, but what options exist for those of us that those of us (for fear of ruining the cars value) have a hard time with cutting into our cars?
I'd love to stiffen up my AAR, but cringe about welding into it.
The Hotchkis ones bolt to the leaf spring pickup point where the rear tire load is transmitted. But check if they work with factory leaf spring boxes (AAR/Hemi/conv/etc)
At the front the Hotchkis connectors weld to the trans crossover. To remove, I think someone can cut the welds, dress the remaining material and even a little bondo and it will be unnoticable. If your car is full undercoasting that would be easy to hide.
Posted By: RTSE4ME
Re: Subframe connector options and opinions - 01/23/12 06:02 AM
Quote:
Quote:
I myself would love to do something, but what options exist for those of us that those of us (for fear of ruining the cars value) have a hard time with cutting into our cars?
I'd love to stiffen up my AAR, but cringe about welding into it.
The Hotchkis ones bolt to the leaf spring pickup point where the rear tire load is transmitted. But check if they work with factory leaf spring boxes (AAR/Hemi/conv/etc)
At the front the Hotchkis connectors weld to the trans crossover. To remove, I think someone can cut the welds, dress the remaining material and even a little bondo and it will be unnoticable. If your car is full undercoasting that would be easy to hide.
Would the Hotctkis connectors clear the side exhaust?
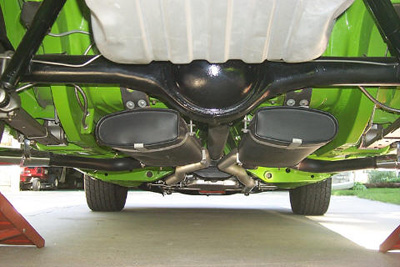
Posted By: Mattax
Re: Subframe connector options and opinions - 01/23/12 03:02 PM
Quote:
I myself would love to do something, but what options exist for those of us that those of us (for fear of ruining the cars value) have a hard time with cutting into our cars?
I'd love to stiffen up my AAR, but cringe about welding into it.
Honestly, in your case I wouldn't worry about it unless you are modifying it for other off-road activities. The e-bodies are already pretty decent. Mitch Lelito's ran very well in National level Solo2 with no connectors in his Challenger. It's also worth noting that for anyone considering running in E Street Prepared (ESP), the connectors can not come through the floor, nor may they be continuously attached to the floor.
My experience with the DC/MP connectors welded front and back (but no other attaching points) is that they do not add alot of stiffness. They are too shallow and really need additional attachment points. A short brace bolted to the rocker to floor brace is a possible answer for those who wish run in ESP or SM. As several posters have already said or implied, the more hieght in the cross section and more attachment points, the more effective the connectors will be. Two inch height in the cross section is a minimum to make them worth anything.
Posted By: Kern Dog
Re: Subframe connector options and opinions - 01/25/12 03:35 AM
NITROUSN:
I really wish that I had your welding skills! You could paint right over those beauties! I need to grind and sand to hide mine!
Posted By: bigtail
Re: Subframe connector options and opinions - 01/25/12 11:42 PM
So, when will be ready to ship? Will you have a tube welded in for the e-brake cable? Will resto ricks carry them? How much? I would buy sub frame connectors and torque boxes as well. Would you offer them as a kit? I have an xv radiator support yoke I will be adding as well. And I plan on a firm feel welded k frame, and poly bushings. c body tie rod ends, welded LCA plates. I want my Challenger SOLID! Please let us know when your connectors are ready, Domingo!
Posted By: JAMESDART
Re: Subframe connector options and opinions - 01/27/12 01:55 PM
to make you feel better, there is a big difference in laying on your back with your car on ramps or jackstands vs standing up and welding with a car on a rotisserie.
Posted By: Valiant_Showoff
Re: Subframe connector options and opinions - 02/02/12 07:08 PM
I like some input on box tubing size recommendation for my street/strip Valiant. Currently running 11.70's, but want the capability in the future to add a cage and run deep into the 10's without needing to modify/re-build the connectors.
I assume the standard is 2"x3" box cut thru the floor and welded along side where it meets the floor pan. What thickness metal is typically used? .083" or 0.120"? I assume A-500 mild steel is suitable?
What about using 2"x2" so that it doesn't protrude so far into the floor? Real world experience with using the smaller tubing? I read above that someone did it and I kind of like that it isn't so intrusive into the interior, but concerned it won't offer the strength improvement needed.
THANKS for the input!
Posted By: jcc
Re: Subframe connector options and opinions - 02/02/12 07:54 PM
Some of the info you seek might be found on chassis mod thread at the top, and compile you your own answer. Sorry I haven't register on my own thread

. I installed a 2x2x.083 not cutting the floors on an early b body, and with combination, noticed little change. Others have much better results, I think as mention earlier in this and other like threads, increased section width/height is much more important to see positive results then greater wall thickness, ie .083 is a good compromise IMO.
Posted By: Mopar Mitch
Re: Subframe connector options and opinions - 02/02/12 08:26 PM
Well said, Matt... SCCA E/Street Prepared rules do not allow cutting of the floor or full-welding to the floor, etc. Only recently a few years ago did they start to allow the front and rear to be welded... prior, they had to be bolted only. Maybe I'll put in the Hotchkiss eventually, or those CPA(?) round/dual ones? Ground clearance is an issue for me, as well. Ultimately, I don't just want to add weight if they won't give a truly good improvement. Chyrsler built their unibody cars very well back then, in my opinion.
Posted By: DaytonaTurbo
Re: Subframe connector options and opinions - 02/02/12 09:50 PM
domningo, we used 2x3" .100 thickness rectangle tube when we did the connectors in my brother's 66 charger. We slotted the front part of the rear sub-frame so the connectors would slide inside, then welded it all back up solid. They don't look like they protrude through the floor much more than yours. Same deal where once you trim away the insulation under the carpet on top of the connectors, you don't know they're there. We just butted the connectors up to the torsion bar crossmember and welded them together instead of notching it like you did.
Before/after difference is night and day. Before if we lifted one corner up with the floor jack, the doors would open/close very poorly. Now with one corner up they open/close like it was on all 4's.

Posted By: TC@HP2
Re: Subframe connector options and opinions - 02/11/12 04:15 AM
This is long, read at our own risk.
Quote:
The first question should be IMO, could someone describe and BACK UP at least, with sound reasoning, what actual forces sub frame connectors resist? I am not questioning many many positive reports of their improvements in ride etc. So are they resisting compression as the rear leafs push forward upon acceleration, are they resisting twist individually, if just under tension we can just use a steel cable, are they preventing a bending moment as front of leaf pushes up upon acceleration with a bending moment provided by the front mass of the car, i.e. engine, etc, are they just straightening out the force path thru 4 right? angle turns from the front hanger to the doorsills back to the TB cross member, etc?.
If we knew what they are resisting, it would be a lot easier to design a solution. I suspect they are doing all the above, but some more than others, but which one? Say if twist was the main force, a large dia tube would be first choice, if bending moment, a tall I beam, yaw? bending, an I beam on its side, etc. My understanding is it needs to be the smallest and lightest shape/size that gets the job done. Anyone can oversize a solution, only a smart designer knows just how much is needed, if you way oversize, you look.....?
Years back member AAR? (patent attorney) had a lengthy thread on Sub-frame connectors, and main conclusion was the larger the crossection of the sub-frame, the stiffer, wall thickness provides a lot less stiffness then crossection increase gives. The installation advantages are numerous with the contour cut-out connectors, and installation ease IMO is their only advantage. Performance wise, compared to a full tube they leave a lot on the table.
Once again, JCC performing the sanity check.
Going back to the muscle car era, from which most of our favorite rides have been derived, the predominate activity involving our automobiles was drag racing. Reading through the literature derived from the era, Mother Mopar, with support of her engineering staff, developed sub-frame connectors to support a car against high powered drag launches and to aid the stock uni-body against axial flexure. It seems 500 horses, drag slicks, a prepared surface, and high rpm launches would conspire over a period of time to bend a car in half. The super stiff front segment of SS spring packs would push up on the passenger compartment floors while pulling down on the shackle mounts. Since the only things holding the middle of the car intact are the door sills, roof, and floor plate, sub-frame connectors were developed to keep roof/quarter seams from splitting, quarter panels form buckling, and back lights from popping out.
In light of that activity, the best connector would be tall, probably bisecting the floor, and provide a great amount of bending resistance against the launch. Think of the floor joists in a house. They are stood on edge to resist deflectionand support weight. Drag race connectors should do the same thing. Of course, anything is better than nothing and even wide 1x2 connectors help out, as do contoured weld in connectors. Obviously 2x3, 3x3, or even 3x1 are better. Using the old bumper jack and open the door test, a simple before and after test will show improvements with the most basic of bolt in connectors installed. Are they optimal, no, but they are better than nothing.
But we aren't talking just drag racing since we have this new forum to play in and we need to consider alternate applications. Looking at research done by XV, DSE, Herb Adams, Julian's, Nascar and others, sub-frame connectors alone don't do a whole lot to increase torsional rigidity. Think of a ladder, there are very strong side rails and lots of cross members, but you can still twist it. So you need to think three dimensionally.
Which segues us into this;
Quote:
Quote:
Aren't the factory rockers in effect thick gauge sorta-square tubes connecting the front and rear sub-frames? If so, what do aftermarket sub-frame connectors do that they don't? Just add strength to the connection because you now have four sub-frame connectors instead of two? Perform some other function?
<snip!>
I thought the same for decades. The I started to notice that newer Mopars -- every B-van, Cherokee, Neon, Stratus, etc. had what was effectively "frame connectors" from the factory, which they started referring to as "uni-frame" design. So I give some simple 2X2" tubing a shot (A-body). Holy cow, the first block, I was fairly well freaked out. The difference in platform rigidity was instantly noticeable.
Rick E.
Actually, yes, you're are somewhat correct in your assumption. However, the rocker panels aren't thick gauge steel. They are the same flimsy stuff that the rest of the body panels are made of. Again, Mother Mopar's research in to this confirmed this and when the Kit car program was developed, the door sills were a dominate structural fixture. However, the also suggested gutting out the inside (floorboard area) and adding square tube bracing to it before tying it in with other structural components. The methods they suggested in this tie in were all bisecting angles that created a car full of triangles. In nature, the strongest inherent shape she has developed is a circle, or sphere. Since cars aren't made with spheres but rather intersecting lines, the next strongest shape, that is compatible with auto design, are triangles. To create rigidity in a car, you need to fill it with triangles. If you look at a traditional sub frame connector, they creates three rectangles out of the cars floor. Rectangles can bend and diamond out of shape. By contrast, triangles resist deformation. Additionally, as a car goes through a corner, it transfers weight diagonally and laterally. Again, triangles assist by providing rigidity where needed while transferring weight were necessary. Obviously this works much better if you think three dimensionally and start creating triangles through-out the car, much like what a current Nascar Cup car looks like. But not all of want to have a street car that looks like a race car. So we compromise and add them in select places without getting to intrusive. If you have ever viewed XV's before and after video of their chassis stiffening it, you'd be amazed what 5 simple pieces of steel can do to a cars foundation.
A big part of why sub-frame connectors works so well is because our cars are put together with spot welds. On top of that, our cars are old, which means those spot welds have had years of flex working against them as well as decades of elements attacking their structural integrity. Consider this, your clothes are stitched together to tighten up seams, close gaps, and provide a better fit. By contrast, our cars are like clothes that are held together with snaps or buttons. Sure they are all together, but they allow gaps and flex. Stitch your car together, just like your clothes, and you eliminate the flexure the requires sub frames to begin with. Julian's did this research on a 1st gen Mustang and through simple rocker sill reinforcement, seam welding, and select bracing, they were able to firm up the Mustang uni-body 70% over stock without installing additional sub frame connectors. SCCA has not allowed seam welding in all stock level competitors because it provides an unfair advantage in structural rigidity. They have only recently relented and allowed sub-frame connectors at all.
A couple of places to read a more in depth analysis of it can be found here:
http://www.pro-touring.com/showthread.ph...;highlight=sn65
http://sn65.com/Chassis%20Design%20101.htm
Posted By: Pale_Roader
Re: Subframe connector options and opinions - 02/11/12 01:37 PM
Thats funny... i was just going to ask why nobody here ever mentions seam-welding. Me an' a well-known local chassis guy/mad scientist used to talk about that. It always seemed like a very solid idea.
Posted By: RTSE4ME
Re: Subframe connector options and opinions - 02/11/12 02:31 PM
I was at a local Porsche track day a few years ago watching a friend of mine. I was checking out some of the GT type race cars and they had welded all the seams. They also welded the top of the cage to the roof. Never saw that before.
Posted By: TC@HP2
Re: Subframe connector options and opinions - 02/11/12 03:13 PM
Quote:
They also welded the top of the cage to the roof. Never saw that before.
I've done that before on my street stock cars. There are classes that outlaw that as well because the the advantage it provides. SCCA and NASA have some that come to mind.
Posted By: radar
Re: Subframe connector options and opinions - 02/12/12 08:17 AM
Posted By: ThermoQuad
Re: Subframe connector options and opinions - 02/12/12 03:40 PM
I did a ton of seam welding on project Charger blacknblue as well as adding the subframe connectors and the "rust repair boxes" to the front frame rails where the torsion bars live.
Some one out there welded up an a body and it worked!
Cop cars got 120 extra welds
it's in the cop car brochures
Aspen/volare/M body cop cars got gussets as well
Posted By: Kern Dog
Re: Subframe connector options and opinions - 02/13/12 08:44 AM
I decided to go ahead and make my own. I used the same type 3x3 .120 wall tube stock that I used on a Duster project. I didn't want to cut the floors, so I made cuts into the tubes to match the floor. I then welded in the open areas to "box" the tubing. They are welded on 3 sides at the front and rear. I also made my own torque boxes out of 14 guage sheet metal. I suppose that the factory torque boxes were built with thinner guage metal, but since I wasn't sure, I just went with what seemed right. I had to reroute the fuel and brake lines since the frame connectors covered the holes that they passed through. Its not fun welding under a car that is on jackstands! While I am fortunate to be in reasonable physical shape, it is still cramped under there. I popped 3 light bulbs from weld spatter. Dang CFL bulbs....THANKS Al Gore....
I'll post a few pictures soon.
Posted By: Silver70
Re: Subframe connector options and opinions - 02/13/12 10:25 PM
Heres a pic of thre xv connectors... I wasn't impressed with the fit at all, they took a ton of grinding to fit. I did smooth them out with some polyester, but afterall the work they did turn out nice. After installing these, my challenger will get some square tube and cut into the floors.
Posted By: Kern Dog
Re: Subframe connector options and opinions - 02/14/12 06:32 AM
I made the conversion to my Lincoln MIG welder from flux core to gas. I was quite happy with the quality of welds compared to the flux core setup. I've found that overhead welding is a little more difficult though. The nozzle tends to trap falling spatter or slag, causing a flow restriction of the gas. I'm sure that there is a way around that. ANY suggestions?
Posted By: curleysracecars
Re: Subframe connector options and opinions - 02/15/12 02:28 AM
Franken...its all in the setup of the machine. You dont want much spatter or slag...you want the weld material sticking to your base material. I know it sounds obvious, but this is MUCH more critical when doing overhead stuff. I HATE it, but only because I dont like the sparks landing on me...I can still weld pretty nice.
Where in GB are you again? Maybe I can come by...it would be nice to meet someone from the forum anyways.
Posted By: jcc
Re: Subframe connector options and opinions - 02/15/12 04:26 AM
That nozzle snot? grease or whatever it is seems to help, at least to remove the splatter you are talking about
Posted By: Kern Dog
Re: Subframe connector options and opinions - 02/15/12 04:38 AM
My welds on level or overhead positions are decent. Its the overhead stuff where I really need improvement.
Nozzle Snot? Is that a product available from a welding supply? This is my first foray into MIG/gas welding. The Flux core had no nozzle to clog. The overhead welds were a little easier that way.
Over the years of working on cars, I've often wondered if my occasional poor results are the result of my limited skills or bad materials/tools. I'm always willing to learn a new method though.
Posted By: jcc
Re: Subframe connector options and opinions - 02/15/12 04:58 PM
Yes any welding supply should have it, its also more properly called Nozzle dip. I think the problem you are having is multifold, dirty hard to clean welds, and the toughness of welding thick to thin, overhead, out of position is just not easy, skill/practice helps, but its still tough.
Posted By: curleysracecars
Re: Subframe connector options and opinions - 02/15/12 05:20 PM
Franken, I use Nozzle spray...I dont like the dip because it drips out of the end of the nozzle when you pull it out of the "tub" it comes in. I use a spray. I spray the material and the nozzle on the gun. As you mentioned, welding on old, dissimilar metals is probably your biggest problem. There is so much crap imbedded in old material, even though it looks clean, it is still usually contaminated to some degree.
Posted By: Kern Dog
Re: Subframe connector options and opinions - 02/15/12 07:36 PM
The horizontal and overhead welding allows the weld to "Build" as I move along, but the overhead areas tend to drip out even though I tried several different settings on the welder. Falling globs of melted metal scare me a little.
I see what you mean... the welding of new & uncontaminated metal to 41 year old Detroit steel could be an issue. On the workbench, welding 2 new pieces together, the welds look great and the beads are not irregular or "Popcorn" like at all. I ran a knotted wire wheel on everywhere I intended to weld, so at least the surfaces looked clean. Its done now though. To finish the trouble areas, I had to do a series of quick ZAPS, then tune it all up with the 4" grinder.
This isn't the last car that I will do, so i am still interested in any other suggestions anyone has. Thank you all!
Posted By: rabid scott
Re: Subframe connector options and opinions - 02/17/12 07:42 PM
Posted By: 74DUSTER360
Re: Subframe connector options and opinions - 04/27/12 02:43 AM
Posted By: Kern Dog
Re: Subframe connector options and opinions - 04/27/12 04:47 AM
Quote:
Check out these bolt in frame connectors - http://unlawfulracing.com/FrameConnectorKits.html
Those look pretty cool. It appears like the rear legs actually fit into the front spring hanger bolts. Obviously this wouldn't work if you had torque boxes, but this setup looks impressive.
Posted By: BrianShaughnessy
Re: Subframe connector options and opinions - 04/27/12 08:58 AM
US Car tool and Auto rust techs torque boxes being installed on Sinnamon. I have MP's on Black Betty... they were good for the day. Had and returned XV sfc's.... they didn't fit at all.
Posted By: BrianShaughnessy
Re: Subframe connector options and opinions - 04/27/12 08:58 AM
from the other end.
Posted By: dangina
Re: Subframe connector options and opinions - 04/30/12 07:53 AM
Quote:
Check out these bolt in frame connectors - http://unlawfulracing.com/FrameConnectorKits.html
I asked them about 8 months ago - said they weren't making any - I see a price so maybe now they are?
Posted By: HemiRick
Re: Subframe connector options and opinions - 05/29/12 05:06 AM
Quote:
However, the rocker panels aren't thick gauge steel.
Here you are wrong, on my 70 Challenger the rocker metal is much thicker than the rest of the sheet metal. I know because my rocker had a big dent and I cut out that section to put in a replacement patch. The patch was regular sheet metal thickness and I ended up beating my original section straight and welding it back in.
Posted By: MadMatt
Re: Subframe connector options and opinions - 06/04/12 05:30 AM
Quote:
Brads70 from protouring mopar offered this idea from his ride which I'll be doing myself - its 1x2" 0.90 tubing with tubes added for strength:
I've been staring at this picture and drooling, but I lack the equipment to replicate them. But I got to thinking, what if you took 2 pieces of 1"x1" tubing and welded them full length side by side to create 1"x2" tubing with a double thickness wall down the center. Would that be just as strong? Since most tubing has slightly rounded corners there would be a natural "groove" that would lend itself to a very solid weld. Any thoughts?
Posted By: Kern Dog
Re: Subframe connector options and opinions - 06/04/12 07:27 AM
While I agree that those 1x3" units with the holes look really cool, I doubt that they have as much strength as a 2x3 or a 2x2. MUCH of the strength is in the vertical plane, and a 1x3 only has 1 inch there. Most agree though that any support added there is a benefit.
Posted By: 68 Sat
Re: Subframe connector options and opinions - 06/05/12 03:49 PM
I used ART for the boxes and frame connectors for my 68 B Body. No problems and they make a difference. Here they are before paint...
Posted By: 68 Sat
Re: Subframe connector options and opinions - 06/05/12 03:55 PM
the money pit