Moparts
Question about fitting subframe connector
Posted By: DrCharles
Question about fitting subframe connector - 12/22/19 11:12 PM
I decided to make my own 2x3 x 1/8" subframe connectors for my '72 Dart Swinger after reading this article:
https://www.bigblockdart.com/techpages/connectors.shtmlUnfortunately I am going to have to notch the rear footwells (and then to weld the floor pan to the connectors, remove the seats and carpeting). The car in the pictures cleared the box tubing but there is no way mine is going to. Oh well, such are body tolerances (especially since some of the floor was replaced by a previous owner, ditto the spring relocation).
However, the left torsion bar crossmember has a "bump" in the rear-facing side. Looks like it was made that way, not bent in an accident.
But now the 2x6 plate on the end of the connector won't sit flat against the crossmember.
Should I hammer it flat? Cut it out? Or notch the end of my connector so the crossmember doesn't require massaging?
Posted By: TJP
Re: Question about fitting subframe connector - 12/23/19 12:19 AM
How does the other side compare?? I'd do some measuring to try and find the root of the problem before banging away with a hammer.
Posted By: TJP
Re: Question about fitting subframe connector - 12/23/19 12:22 AM
Looking at it again, is the bump you're referring to there to angle the e brake cable ??
Posted By: DrCharles
Re: Question about fitting subframe connector - 12/23/19 12:25 AM
The right hand side doesn't have that curved protrusion in the crossmember, and the connector is the same length on both sides

So it would fit except for the rear footwell interference.
Posted By: krautrock
Re: Question about fitting subframe connector - 12/23/19 01:35 AM
looks like it was made that way.
i would make the subfraem connector fit the shape, or make the subfraem connector with a bit of an angle so it goes to the left of that bump, but it seems you've already cut that tubing so that might not be an option now...
Posted By: DrCharles
Re: Question about fitting subframe connector - 12/23/19 01:56 AM
Looking at it again, is the bump you're referring to there to angle the e brake cable ??
No... there is some distortion in the picture with the closeup setting on my old camera. The e-brake cable hole actually comes straight through the t-bar crossmember, next to the bump.
I'll probably just notch the end of my connector on that side. It only has to sit flush with the bottom of the crossmember - the required notch isn't that big nearer the bottom anyway.

I don't feel like taking more of the car apart just now (3rd member is at Dr. Diff) so the connectors can wait a while...
Posted By: forphorty
Re: Question about fitting subframe connector - 12/23/19 03:33 AM
The bulge under the E brake cable is factory. You could put a slice in it, beat it flat and weld it up. On my duster I used 2x3 . At the rear, rather than cut into the rear floor pan, I cut out a 1/2 tall strip lengthwise making it a 1.5x3 in the rear floor area and welded it back together . I cut it with a curve so it made a nice transition at the rear pan. Cardboard templates are your friend with this kind of stuff.
Posted By: DrCharles
Re: Question about fitting subframe connector - 12/23/19 03:57 AM
Thanks. That is another option, but I'm already giving up stiffness by mounting the 2x3 tubing horizontally... making part of it 1.5 would be even weaker (although still better than just the unibody).
Also it's easier to cut the sheet metal of the floor pan than the 1/8 wall tubing. I don't own a plasma cutter and using a cutoff wheel has already gotten old

What about just lowering the rear of the connector 1/2" so it touches the floor pan but doesn't have to go up through it?
Posted By: forphorty
Re: Question about fitting subframe connector - 12/23/19 04:52 AM
I here ya on the cutoff wheel being tedious. I used the plasma cutter from work. You can just push the connecter up against the floor pan but it will hang down about a 1/2 lower than the rail. I wasn't too worried about the strength of the 1.5 section as most of the old connecters like the MP ones are only 1.5x2. Plus I welded mine to the floor pan where it touched. Originally, I didn't intend on welding to the floor because I wasn't keen on scraping off a bunch of undercoating in the area. In the end, I got carried away and removed all the undercoating off the bottom of the car. Being told that undercoating typically weighs 50 to 100 lbs was my motivation.
Posted By: dvw
Re: Question about fitting subframe connector - 12/23/19 01:38 PM
I'ma firm believer that the rail thru the pan welded fully is the stiffest. I cut the bottom out of the rear rail. Drilled the spot welds holding the remaining rail to the floor pan at the front. Then slid the 2x3 into the rear rail "sides". Clamped the the sides to the tube . Then welded it all back up thru the previously drilled spot weld holes. Plug welded the rail sides as well. .This pulls the frame rail sides in about 1/8" but everything fits nice and tight. Cut the slices in the floor narrow and work your way up to size.
Doug
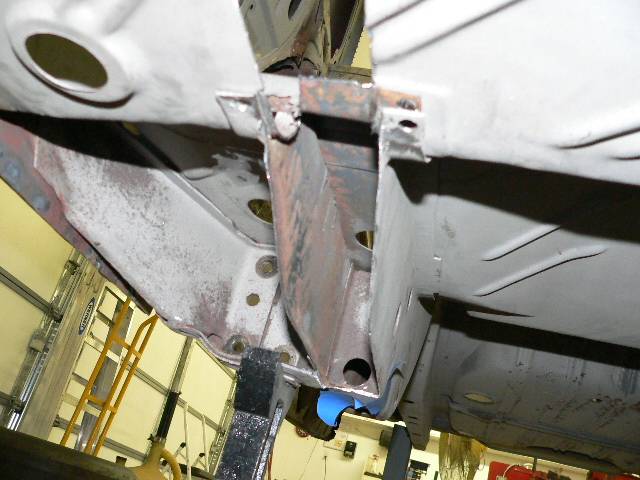
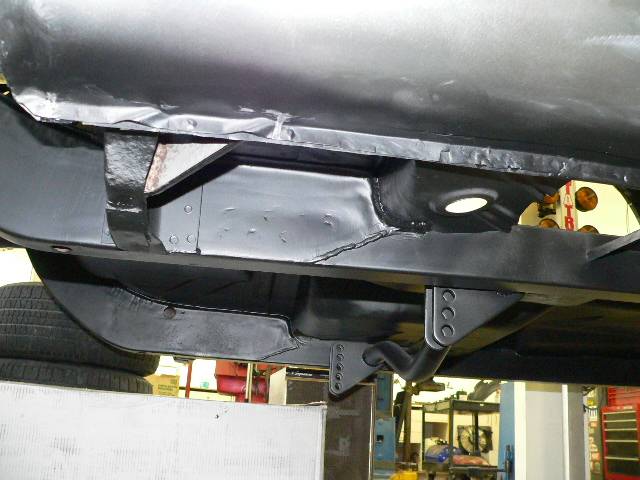
Posted By: 76Beeper
Re: Question about fitting subframe connector - 12/23/19 06:23 PM
I agree with dvw that going thru the floor makes it much stronger.
Mine started out as bolt in connectors. But they hung too low in the back (they sat below the rear frame rail).
So I modified them to fit up thru the floor.
This is on a 1971 B-body.
.jpg)
Posted By: topside
Re: Question about fitting subframe connector - 12/23/19 07:12 PM
Yup, into the rear rails and the floor involves more of the structure.
IIRC, 2 x 2 is a nice fit on an early B into the rear rails but not needing the floor cut.
1/2" or so coming up through the floor isn't noticed under the carpet, though, that's how my Duster is.
An alternative to cutting the floor is a slight bend in the tie tube, but straight is arguably stronger than bent.
As for the crossmember bulge, fit the subframe tube & tie plate to it.
Posted By: CMcAllister
Re: Question about fitting subframe connector - 12/23/19 07:25 PM
I'ma firm believer that the rail thru the pan welded fully is the stiffest. I cut the bottom out of the rear rail.
True. But I'm not quite that invasive on a typical deal, especially if we're keeping the leaf springs. We use a 2x3 and section it into the rear seat floor area so it is half above the floor and half below at the rear rail area. Open up the front of the rail where it joins the floor, half above, half below the floor so the connector will slide into the front of it. The rail can still be drilled up for plug welds if you like. Section the floor so the connector will rotate up and bump into the rear of the torsion bar x-member and just touches the top flange where the floor is spot welded to it. Everything will be above the pinchweld of the rocker this way. "Outriggers" from the connector to the inside of the rocker can be installed to mount the main hoop and diagonals rather than using plates. Makes for a stiff platform.
This will take some time to layout and cut to get the connector in parallel to the CL of the car and keep the fits tight for welding. But the results are worth the time.
Wish I had taken photos of some of this stuff.
Posted By: DrCharles
Re: Question about fitting subframe connector - 12/23/19 09:49 PM
Nice work! But since my car is now complete except for the connectors, it'll be hard to put on a rotisserie (not only that, I don't have the floor space... or a rotisserie)

Not to mention that my welding skills even on a table in-position are mediocre...
The springs are already relocated into the frame rails, and I plan to purchase the appropriate Caltracs (#4209 I think). So even if I lower the rear of the subframe connectors by 1/2" and don't cut the floor, they won't present a problem with ground clearance relative to the Caltrac front plates. Could still weld the connector to the floor pan at some later time also, or add angle iron brackets welded between the connector and the pan.

I didn't put the heavy bench rear seat back in, either.
Posted By: jcc
Re: Question about fitting subframe connector - 12/23/19 11:18 PM
Not sure what the design goal here is, or the cars intended use. I would Not "roll Over" the 2x3. I would not use 1/8"/11g tubing. 2x2 would solve a lot of issues I suspect. Nobody here in over a decade can clearly delineate what forces the SFC's are exactly resisting, so the thinking "it can't hurt" likely applies. I would weld the 11G? end plates onto the TB crossmember first, and also add a center hole to weld/hold down the center of the plate, and then weld /fit the SFC to that, and weld in place. You may have a tough time welding the top fully, but anything you get on that surface would help.
Here is one of my cars with 2x2, 3 pics starting at pic #8:
https://board.moparts.org/ubbthread...e-62-polara-500-cruiser.html#Post1554319
Posted By: DrCharles
Re: Question about fitting subframe connector - 12/23/19 11:50 PM
I would Not "roll Over" the 2x3
What does this mean?

I would not use 1/8"/11g tubing.
What
would you use?
Posted By: dvw
Re: Question about fitting subframe connector - 12/24/19 12:29 AM
Posted By: jcc
Re: Question about fitting subframe connector - 12/24/19 03:34 PM
I would Not "roll Over" the 2x3
What does this mean?

I would not use 1/8"/11g tubing.
What
would you use?
Your attached pic looks like to me like you have the vertical dim as 2" and the horizontal plane 3". That is not a very common orientation, and I described as "rolled over".
I would use 14g in this application, 16g is too light, and 14g is a common available size, it will also be easier to weld up to floor sheet metal, and 11g is overkill unless there is a specific need, IMO.
Posted By: DrCharles
Re: Question about fitting subframe connector - 12/24/19 09:12 PM
Did you read the BBD Tech Pages article I linked in my first post?

The rear frame rails are a near perfect fit for the ID of a 2x3" 1/8-wall box tube when it's oriented that way. Which is also readily available at both steel places in my area... don't think they had anything but 1/16 and 1/8 anyway.
Although the connector would be stronger in flexion if oriented vertically, much longer floor cuts/welding would be required also.
Anyway I originally just asked whether to flatten the curved protrusion on the left T-bar crossmember or to notch the plate/connector

But this is one of the topics (like 8-3/4 vs. Dana) which is guaranteed to start a lively discussion
Posted By: BigBlockMopar
Re: Question about fitting subframe connector - 12/24/19 09:45 PM
Before all this, I would start by 'reconnecting' the floorboards to the crossmember again (since someone replaced the floorboards but 'forgot' to weld them properly).
Posted By: DrCharles
Re: Question about fitting subframe connector - 12/24/19 09:57 PM
Good point. What is the least invasive way to accomplish this? Hammer the two surfaces together and spot (plug) weld?

Edited to add: If I end up going as fast as I'm hoping, I will need a six-point roll bar anyway. If that's tied into the subframe connectors, are the floor pan welds still important?
Posted By: BigBlockMopar
Re: Question about fitting subframe connector - 12/24/19 10:23 PM
Spot welds are factory. I would run a full bed along the edges on both sides of the crossmember.
I did (had to do) so on my '73 Dart because I partly removed the upper part of the crossmember in the tunnel for a 518-transmission. Over time the factory spotwelds were tearing loose from the floorboard.
Remember the (dynamic) weight of the transmission/engine is leaning down on that crossmember all the time, as well as the torsion bars are putting a varying rotation torque/force onto the anchors.
Posted By: Dave_J
Re: Question about fitting subframe connector - 12/25/19 05:41 AM
I drilled small holes from under thru the crossmember's web as it folds out to the floor pan. Then on the top side I used sheetmetal screws to suck the floor pans down tight and then back under I stitch welded the pans to the x-member. Then I removed the sheetmetal screws and just welded the holes up.
But drilled holes and Clico's should also work.
Posted By: TC@HP2
Re: Question about fitting subframe connector - 12/25/19 08:39 PM
Nobody here in over a decade can clearly delineate what forces the SFC's are exactly resisting, so the thinking "it can't hurt" likely applies.
RE the snipped out section above, I thought at one point over all these years we had talked about how Mopar's Hustle Parts engineers had developed the sub-frame connectors to resist the beaming motion of drag launches way back in the early 70s.
Did you read the BBD Tech Pages article I linked in my first post?

The rear frame rails are a near perfect fit for the ID of a 2x3" 1/8-wall box tube when it's oriented that way. Which is also readily available at both steel places in my area... don't think they had anything but 1/16 and 1/8 anyway.
Although the connector would be stronger in flexion if oriented vertically, much longer floor cuts/welding would be required also.
Anyway I originally just asked whether to flatten the curved protrusion on the left T-bar crossmember or to notch the plate/connector

But this is one of the topics (like 8-3/4 vs. Dana) which is guaranteed to start a lively discussion
IMO, unless rules require it or you are pursing a more full frame approach, there really isn't the need for .125 wall structural reinforcements pieces in a uni-body construction. However, it is a common approach taken by many that if large is good, bigger is even better. If one is willing to add weight for structural improvements, much greater gains can be made with stitch welding factory structure over adding a bunch of eight inch wall structural components. Since your car is complete, proceed with the thick wall connectors and enjoy the increase in rigidity they will provide.
Posted By: B1MAXX
Re: Question about fitting subframe connector - 12/25/19 09:24 PM
they provide a good place to land the kick in's from the main hoop.
Posted By: Dave_J
Re: Question about fitting subframe connector - 12/25/19 10:57 PM
And for the road racing group, a place to tie the outter unibody to inside.
Posted By: jcc
Re: Question about fitting subframe connector - 12/26/19 02:59 PM
Nobody here in over a decade can clearly delineate what forces the SFC's are exactly resisting, so the thinking "it can't hurt" likely applies.
RE the snipped out section above, I thought at one point over all these years we had talked about how Mopar's Hustle Parts engineers had developed the sub-frame connectors to resist the beaming motion of drag launches way back in the early 70s.
I agree, but in drag race beaming improvement is the single objective often sought, for the OP, laying the 2x3 over is rather inefficient from a design standpoint in that goal, and the main basis for my comment. And I wonder, if the prospective SFC installer is not nearly lifting the front tires on a launch, not sure "beaming" issues should be their main concern. I'm more focused on torsional improvement, and once that direction is decided, it seems there is a plethora of ideas of the various solutions that SFC's actually contribute to the problem, albeit including some contribution with "beaming" issues.
TC, you are seldom one I ever seek to technically argue with, your continuous contributions here are well regraded, and I hope this is not one of them.
Posted By: TC@HP2
Re: Question about fitting subframe connector - 12/26/19 04:51 PM
Nah, not looking for a debate on this one. Just recalling when we did really dig into the sub-frame connector piece and couldn't find much supporting evidence for torsional rigidity increases. Probably best not to blur any lines for the more casual tech readers.
Posted By: Dave_J
Re: Question about fitting subframe connector - 12/26/19 10:58 PM
Laying the tube flat may not be as good as standing it up but its still better than no SFC, IMHO.
I'd just spend the 2 hours to remove the seats and carpeting to fit it standing up, weld it in good and then 2 hours putting the carpet and seats back in....
Posted By: CMcAllister
Re: Question about fitting subframe connector - 12/27/19 09:38 PM
Nobody here in over a decade can clearly delineate what forces the SFC's are exactly resisting
How about - any that cause the entire body/chassis/suspension mounting points to deflect from it's static shape and dimensions. SFCs are only a part of the picture. A well designed cage structure that incorporates the original stamped sheet metal to further strengthen and stiffen the entire assembly, is the other part. There is substantial strength in those body panels; use them. Don't just cut a hole in the floor, pass a bar through it and patch it with a piece of aluminum. Fit it correctly to the sheet metal and weld it up. “The whole is greater than the sum of its parts.”
Why hang expensive suspension components and try to tune them with any predictable results when they're attached to a flimsy structure? I've seen high end Super Stock/Comp cars that were cleaned and had all the individual spot welded body parts stitch welded together before anything else is done. Time and money? Yes. But a substantial and verifiable improvement. Stop thinking of it as a cage stuck inside the body and look at it as a complete structure.
2x2 maybe if we insist on not sectioning it into the floor. 2x3 stood on end is much stiffer and allows for more of the floor to be sectioned into it and the cage structure to be attached directly to it. .083 wall is plenty substantial. We're still concerned about weight.
Posted By: krautrock
Re: Question about fitting subframe connector - 12/27/19 09:44 PM
i think the common 2x3 tubing is usually 11ga, which is .120 wall.
Posted By: CMcAllister
Re: Question about fitting subframe connector - 12/27/19 10:20 PM
i think the common 2x3 tubing is usually 11ga, which is .120 wall.
Yep. You have to look for or order the .083. UPS will ship 8' lengths. Saves almost 10lbs for 8'. It's also available in .065.
Posted By: DrCharles
Re: Question about fitting subframe connector - 12/27/19 11:31 PM
I'm not
that concerned about weight, except my own... being embarrassingly close to 300 lb with a helmet on

So the extra 20 lb of steel isn't that big a deal, since it's not a class racer

Once I get the aluminum heads and the bolt-on glass hood installed, that'll knock off a lot more. The best thing I can do is lose the 50+ lb of excess body weight that I already should have...
Posted By: CMcAllister
Re: Question about fitting subframe connector - 12/28/19 12:55 AM
If we are spending money for fiberglass and aluminum, I would think that saving 10-12 pounds and probably saving a little money as well would be an easy decision.
Posted By: DrCharles
Re: Question about fitting subframe connector - 12/28/19 01:34 AM
Well, it's primarily a street car with possible occasional strip use. "We" spent the money for aluminum in order to increase performance (via porting). Iron heads are not only limiting but ridiculously expensive to port to relatively modest aluminum head levels. The weight loss is a bonus. Similarly, the glass hood has a scoop built-in to allow more carb/manifold clearance and admit more cool air, without having to spend money and time hacking up the original flat steel hood or paying a body man to do it. Again, the weight loss is a bonus.
You pointed out in your earlier discourse that structures work as a system. Same with every decision to buy, modify or replace parts - none of that happens in isolation.
Posted By: Dave_J
Re: Question about fitting subframe connector - 12/28/19 01:37 AM
I know dealing with 8 foot sections of 2x3 boxed tubing building motorcycle trike frames we found little difference in flex between 0.120 and 0.095 and 0.083 when tied in with the other frame parts all diagonally braced. And the diag's were all 0.063" DOM round.
But we are talking a 800 pound trike and not a 3200 pound car. But then again the SFC's are not real structural in most use. I bet you could get about the same effect with a stick of 1 1/2" 0.095 DOM buired half way into the floor pan and stitch welded to the pan.
Posted By: CMcAllister
Re: Question about fitting subframe connector - 12/28/19 03:17 AM
These days, most serious builds and those that need to have an SFI tag are all round tube. And it's 4130. 1.500x.065 frame rails but there is also plenty of diagonals and bracing as well.
Posted By: TC@HP2
Re: Question about fitting subframe connector - 12/28/19 04:00 PM
I know dealing with 8 foot sections of 2x3 boxed tubing building motorcycle trike frames we found little difference in flex between 0.120 and 0.095 and 0.083 when tied in with the other frame parts all diagonally braced. And the diag's were all 0.063" DOM round.
But we are talking a 800 pound trike and not a 3200 pound car. But then again the SFC's are not real structural in most use. I bet you could get about the same effect with a stick of 1 1/2" 0.095 DOM buired half way into the floor pan and stitch welded to the pan.
Using the totally unscientific method of jacking up one corner to change the tire methodology, I got the same observed stiffening results from .120 2x3 square tube installed logitudinal as from an Xed structure of 1.5 x.090 DOM round tubing. Or course the X arrangement did not allow much room for exhaust and may not be practical in a street car.
Posted By: Dave_J
Re: Question about fitting subframe connector - 12/28/19 07:31 PM
The guy I was working with made ladder frame sections 8 foot long. At the rear it was 18 inches tall and the top tubes were curved down to 12 inches up front. As said all the diag's were 5/8x0.063 DOM. He then placed the single ladder on blocks and set a dial indicator under and loaded 300 pounds in the center to measure deflection. From memory, the difference between 0.120" and 0.085 was about 0.25 inch. In a bounce, he lifted up on the center and dropped it 4 times, I think it was like 7/16 inch difference.
But in these tests he did not do a 100% full weld on the diag's so there may have been some loss of rigidness.
He ended up using 2 of the 1.5x0.085" tubes on the bottom and 2 of the 1.5x0.063" tubes on top.
"This thread is worthless without Pic's" Yes I lost all those pictures when a hard drive failed. I'll see if he has pictures on the Web of the build.
Posted By: jcc
Re: Question about fitting subframe connector - 12/28/19 08:10 PM
The problem that sticks out to me in your ladder bar example, the thicker wall thickness main chord might mainly just strengthen the welded node connection between the larger tubing and and the smaller 5/8" D diagonal tubing, and that accounted for a lot less of the deflection, would be my guess.
Posted By: dvw
Re: Question about fitting subframe connector - 12/29/19 12:59 AM
These days, most serious builds and those that need to have an SFI tag are all round tube. And it's 4130. 1.500x.065 frame rails but there is also plenty of diagonals and bracing as well.
Agreed,two different style builds. Those that are milder using the body and cage as one structure. And those trying to be as light as possible being 25.5D compliant. The sheet metal is merely visual and not much structure.
Doug
Posted By: jcc
Re: Question about fitting subframe connector - 12/29/19 01:07 AM
I disagree. SFC IMO mainly improve/shortcut the original torturous load path of transmitting forces from the front leaf spring mount, to the rear torque box, to the outer door sill, to the front torque box, to the TB cross member, to the front frame longitudinal.
The original designers were forced to made a number of compromises.
Posted By: polyspheric
Re: Question about fitting subframe connector - 12/30/19 03:34 PM
Differences in wall thickness affect stiffness (bending resistance) in direct proportion: .120" wall is 33% more than .090", etc.
The vertical dimension is far and away the most important. 3" tall by 2" wide is 90% more rigid than 2" tall by 3" wide (47% stiffness is lost by rotating).